Introduction
The advent of rolling mill technology and its development during the first half of the nineteenth century also heralded in the industrial manufacture of tube and pipe. Initially, rolled strips of sheet were formed into a circular cross section by funnel arrangements or rolls, and then butt or lap welded in the same heat (forge welding process).
Toward the end of the century, various processes became available for the manufacture of seamless tube and pipe, with production volumes rapidly increasing over a relatively short period. In spite of the application of other welding processes, the ongoing development and further improvement of the seamless techniques led to welded tube being almost completely pushed out of the market, with the result that seamless tube and pipe dominated until the Second World War.
During the subsequent period, the results of research into welding technology led to an upturn in the fortunes of the
welded tube, with burgeoning development work ensuing and wide propagation of numerous tube welding processes. Currently, around two thirds of
steel tube production in the world are accounted for by welding processes. Of this figure, however, about one quarter takes the form of so-called large-diameter line pipe in size ranges outside those which are economically viable in seamless tube and pipe manufacturing.
Seamless Tube and Pipe
The main
seamless tube manufacturing processes came into being toward the end of the nineteenth century. As patent and proprietary rights expired, the various parallel developments initially pursued became less distinct and their individual forming stages were merged into new processes. Today, the state of the art has developed to the point where preference is given to the following modern high-performance processes:
The continuous mandrel rolling process and the push bench process in the size range from approx. 21 to 178 mm outside diameter.
The multi-stand plug mill (MPM) with controlled (constrained) floating mandrel bar and the plug mill process in the size range from approx. 140 to 406 mm outside diameter.
The cross roll piercing and pilger rolling process in the size range from approx. 250 to 660 mm outside diameter.
Mandrel Mill Process
In the Mandrel Mill Process, a solid round (billet) is used. It is heated in a rotary hearth heating furnace and then pierced by a piercer. The pierced billet or hollow shell is rolled by a mandrel mill to reduce the outside diameter and wall thickness which forms a multiple length mother tube. The mother tube is reheated and further reduced to specified dimensions by the stretch reducer. The tube is then cooled, cut, straightened and subjected to finishing and inspection processes befor shipment.
Production | ASTM A106 Seamless Steel Pipe SCH10-XXS |
Brand | Hebei Gee Pipe Mill Co. Ltd. |
Standard | ASTM ,API5L,ASME,ANSI,GB,DIN,JIS,BS,etc. |
Out Diameter | 1/2"--24" |
Wall Thickness | SCH5--SCH××S |
Grade | 10# 20# 45# 16Mn A53 A106 A269 A312 A179-C A213 Q195 Q215 Q235 Q345 |
Length | 5.8m--11.8m or according to customer's requirementv. |
MOQ | 5 tons |
Plade of Origin | China |
Port | Tianjin Xin Port |
Technique | Cold Drawn |
Usage | 1.Low and middle pressure fluid transportation pipeline 2.Casing Tube 4.Petroleunm and natural gas industry 5.Chemistry industry 6.Electric industry |
Package | 1.Bundle packing. 2.Bevelled end or plain end or warnished as per buyer's requestments. 3.Marking: as per customer's requests. 4.Painting varnish coating on the pipe. 5.Plastic caps at ends. |
Delivery Time | 15-30 days or as clients reqestments. |
Supply | 5. hot-rolled steel pipe |
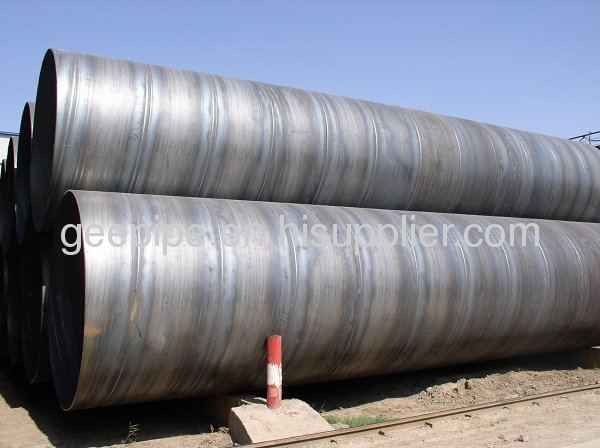